Banco de prueba de eje electrónico
The Challenges of E-Axle/ Axle/ electric drive unit (Edu)
Las unidades eléctricas están en el corazón de ambos vehículos eléctricos (Bevs) y vehículos eléctricos de celda de combustible (Fcev), As manufacturers face growing demands for Innovations in e-drive development are driving deeper integration of inverters, e-motores, and transmissions into a single housing of an e-axle sub-system, Nuestras soluciones integrales respaldan cada fase del ciclo de vida del proyecto, desde el desarrollo conceptual hasta la implementación y la operación. Estas soluciones están diseñadas para atender a una amplia gama de vehículos., incluyendo vagones de pasajeros, así como vehículos comerciales ligeros y pesados.
El sistema de accionamiento de un vehículo eléctrico (EV) comprende varios componentes clave. Temperature and Pressure Chamber can be added, Central para esto es el eje electrónico o la unidad de accionamiento eléctrico (Edu), que integra el motor eléctrico, transmisión, e inversor. Mientras proporcionamos soluciones de prueba dedicadas para cada componente individual, Es igualmente importante probar el eje electrónico completamente ensamblado para identificar y abordar posibles defectos relacionados con el ensamblaje, como el ruido, Vibración, Dureza (Nvh) y EMC/EMI pruebas, que afecta significativamente la satisfacción del conductor y el pasajero y garantiza la seguridad del vehículo.
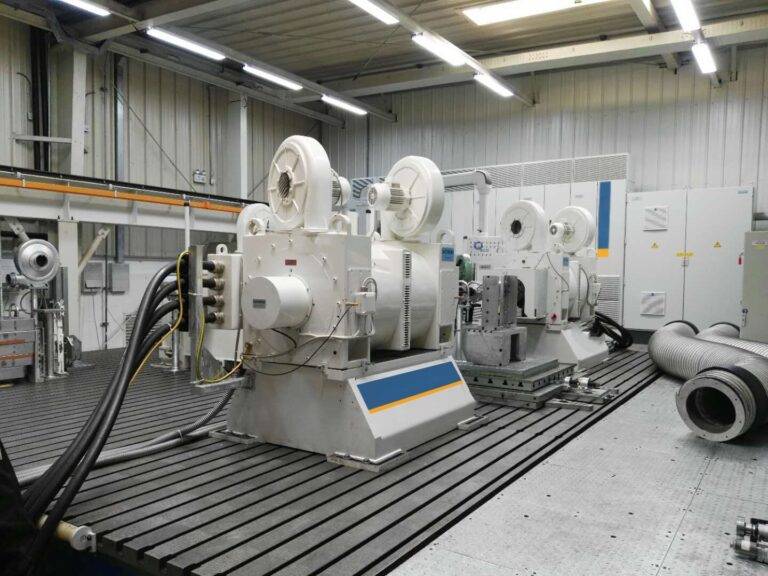
Multi Axles EMC Testing Solution
Multi axles EMC dynamometer systems are used for testing E-drive or E-axle. This testing arrangement is closer to the actual state of the vehicle, and the test results are more realistic. Benefits as below:
- High dynamic response for direct connection.
- Original e-axle testing, without any changing. Match the real vehicle environment.
- Reasonable load device could fit for multiple UUT test at the same TB. Include heavy duty e-motor, light duty e-motor and e-axle.
- increasement of one free-standing EMC dynamometer, testing the hybrid or extended range electric drive system.
Type | nmax(rpm) | Trated(N.m) | Prated(KW)norte | nrtated(rpm) | n2(rpm) | Pmax(KW)@ nmax | Cooling |
EC300-12/10 | 12000 | 1000 | 300 | 2865 | 12000 | 300 | Air |
EC300-10/12 | 10000① 20000② | 1300 600 | 300 | 2204 4408 | 10000 20000 | 300 | Air |
EC300-10/20 | 10000 20000 | 2000 600 | 300 | 1432.5 2865 | 7500 15000 | 220 | Air |
EC300-10/25 | 10000 20000 | 2500 600 | 300 | 1146 2292 | 7500 15000 | 220 | Air |
EC400-08/30 | 8000 20000 | 3000 600 | 400 | 1273 3182.5 | 6000 15000 | 300 | Air |
EC400-07/35 | 7000 20000 | 3500 600 | 400 | 1091 3400 | 5000 14286 | 350 | Air |
EC450-06/40 | 6000 20000 | 4000 600 | 450 | 1074 3580 | 5000 16667 | 350 | Air |
EC500-06/45 | 6000 20000 | 5000 600 | 500 | 955 3183 | 4000 13333 | 400 | Air |
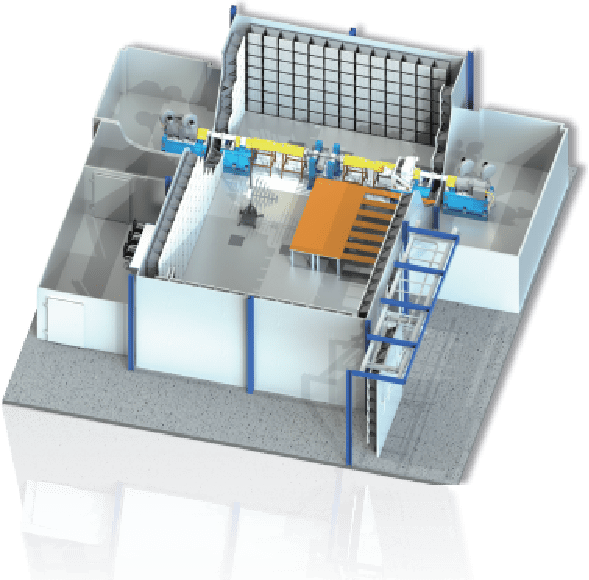
What is an E-Axle / Axle Test Bench?
An E-Axle Test Bench is a highly specialized testing system for evaluating the performance, durabilidad, and efficiency of electric vehicle (EV) axles and hybrid vehicle axles. This system is essential for R&D, certification, and quality control, simulating real-world conditions to measure key parameters such as torque, velocidad, potencia de salida, and energy consumption. These test benches are engineered for precision, allowing automotive manufacturers to meet stringent industry standards and regulatory requirements.
Core Components of the E-Axle Test Bench:
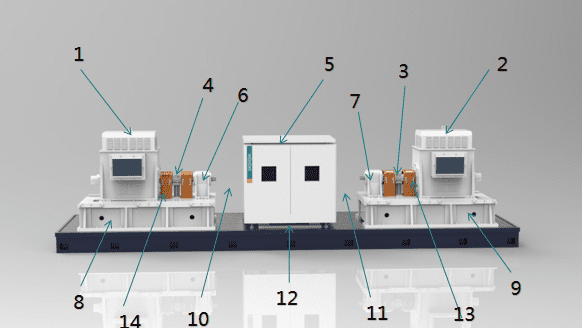
Nuestro E-Axle Test Bench features a modular and highly customizable design that can be adapted for various axle types, including single-wheel, dual-wheel, and full-drive configurations. Below are the core components of the system and their functionality:
1. Eléctrico Motor Unit:
Key Features:
Big Power output up to 500 kW and can be customized more power output
Adjustable torque and speed for various axle configurations
Highly efficient and energy-saving design
Supports dynamic load simulation for electric, híbrido, and traditional vehicles
2. Rollers (48 Inches and Customizable size)
Function: The rollers serve as the contact surface for the vehicle’s tires, enabling the simulation of driving conditions. The rollers are designed to replicate various road surfaces and allow the measurement of the axle’s ability to handle torque, fuerza, and rotational speed under load.
Key Features:
Roller Size: 48 inches diameter (1219.2 mm) to accommodate a wide range of vehicle tires
Roller Material: Robust, anti-wear material designed to simulate realistic road conditions
Customizable Width: Options for different axle configurations (1×2, 2×2, 2×4, 4×4)
3. Torque Sensors and Speed Sensors
Function: These sensors continuously monitor the torque and rotational speed on the axle, providing real-time data for accurate analysis. The torque sensors measure the force applied to the axle, while the speed sensors measure the rotation speed. Together, they offer detailed insights into the efficiency and performance of the axle under different load and speed conditions.
Key Features:
Real-time monitoring of axle performance
High-precision sensors with minimal error
Feedback for energy consumption analysis and efficiency testing
4. Load Control System of E-Axle Test Bench
Function: This system precisely adjusts and controls the load applied to the axle, allowing the test bench to simulate various driving conditions such as acceleration, deceleration, and constant speed. The load control ensures the system can simulate both low and high-performance driving cycles, which are essential for testing a wide variety of axles.
Key Features:
Adjustable load settings for different testing conditions
Integrated with the motor and sensors for seamless operation
Simulates various terrain conditions including uphill, downhill, and flat surfaces
5. E-Axle Test Bench Environmental Control System
Function: The environmental control system regulates the temperature and humidity in the test area, simulating different climates. This is essential for durability testing, as axles are tested under extreme conditions, ensuring that they will perform reliably under various environmental factors such as heat, cold, and moisture.
Key Features:
Wide temperature range from -40°C to 100°C
Humidity control for accurate environmental testing
Integrated cooling and heating system for consistent test conditions
6. Control and Data Acquisition System (DAQ)
Function: The data acquisition system collects and processes test data, providing real-time feedback on the axle’s performance. It monitors key metrics like torque, potencia de salida, eficiencia, energy consumption, and temperature. The system integrates with the motor control unit for synchronized testing and ensures compliance with industry standards.
Key Features:
Automated testing protocols and results analysis
Real-time data logging with visual output for easy interpretation
User-friendly interface for configuring test parameters and reviewing results
7. Customizable Test Interface of E-Axle Test Bench
Function: This feature allows the user to configure the test setup for different types of axles and vehicle configurations. It includes adjustable test protocols for testing passenger vehicles, trucks, and hybrid systems, making it a versatile tool for a wide range of automotive manufacturers and R&D labs.
Key Features:
Modular design for customization based on vehicle type
Supports a variety of test cycles and performance evaluations
Easy integration with existing testing systems
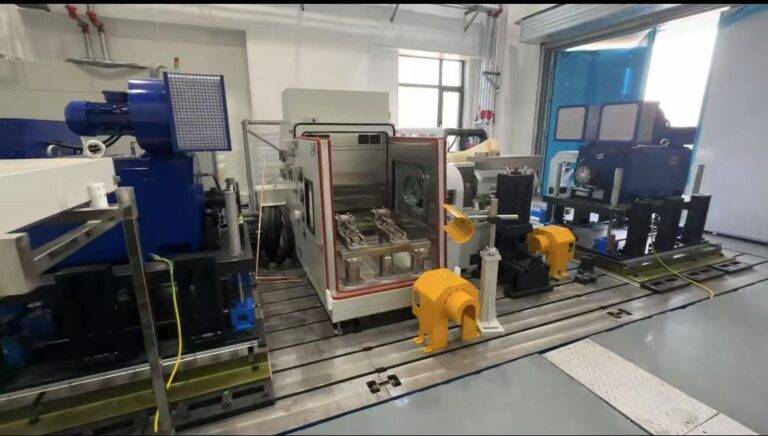
Modular Heavy-Duty Electric Axle Test Bench for Reliable UUT Evaluation
Nuestro Heavy-Duty Integrated Electric Axle Test Bench is a modular, scalable testing solution designed to evaluate the performance and durability of electric drive units in trucks, buses, and off-road vehicles. By simulating real-world operating conditions, it enables comprehensive service-lifetime and thermal endurance testing, ensuring your electric axles meet the toughest industry demands.
Beneficios clave:
✔ Adaptable for diverse UUT (Unit Under Test) configurations
✔ Real-world simulation for accurate reliability validation
✔ Scalable design for flexible testing requirements
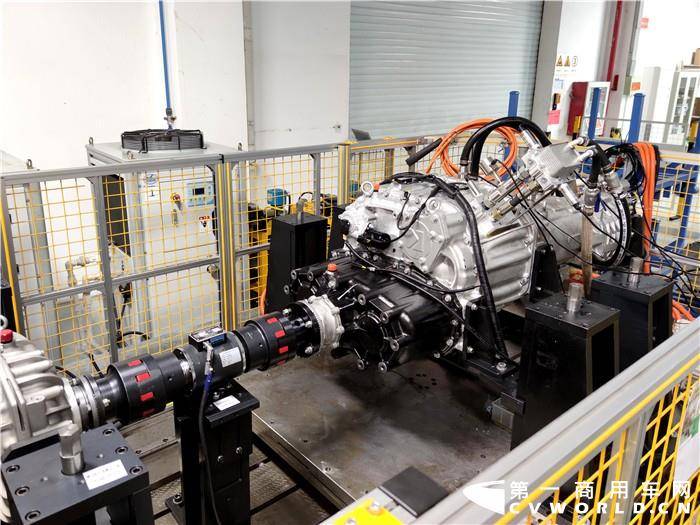
X-in-1 Electric Axle Test Bench for Temperature & Lifespan Certification
El X-in-1 Electric Axle Test Bench is engineered for precise temperature aging and service lifespan certification of electric drive units. It integrates pre-configured duty cycles with standardized testing protocols, allowing manufacturers to assess long-term durability and thermal performance under controlled conditions.
Key Features:
✔ Seamless integration of standardized test cycles
✔ Reliable certification for harsh operating environments
✔ Optimized for efficiency in endurance testing
Advanced Testing Techniques for Electric Axle Performance Validation
Nuestro electric axle test bench leverages cutting-edge mechanical and electrical testing methods, incluido:
Integrated control system for precise parameter regulation
Dual load machines for dynamic performance simulation
Conditioning unit & Fuente de alimentación de DC for consistent testing conditions
Flexible automation for systematic, repeatable test procedures
Why It Matters:
✔ Closed-loop torque & speed control for accuracy
✔ Enhanced safety with galvanically isolated DC power
✔ Compact, pit-free installation for quick deployment
Space-Saving & Efficient Electric Axle Test Bench Design
Designed for easy industrial integration, our test bench eliminates the need for specialized flooring or pits, thanks to its compact, self-contained cabinet design. Con advanced converter technology, it reduces grid connection complexity while maintaining high-performance testing capabilities.
Installation Advantages:
✔ Plug-and-play setup for rapid deployment
✔ Minimal footprint, maximum efficiency
✔ Optimized for fast, hassle-free testing
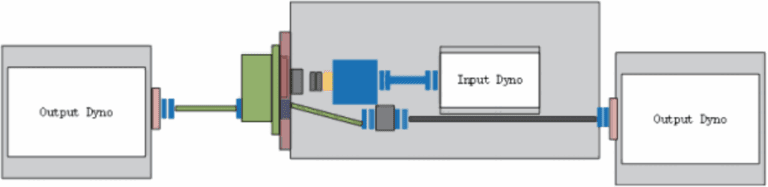
Applications of the E-Axle / Axle Test Bench:
Performance Testing: Evaluate maximum speed, potencia de salida, and efficiency of the axle.
Durability Testing: Simulate long-term use under various road conditions to test reliability and lifespan.
Energy Efficiency: Measure energy consumption and regenerative braking efficiency for electric and hybrid vehicles.
Prueba de emisiones: For vehicles with hybrid drivetrains, ensure that emissions are within regulated limits.
Regulatory Compliance: Ensure compliance with automotive and environmental regulations, including EPA and EU standards.
Custom Testing: Tailored testing for specialized vehicle applications such as off-road vehicles, trucks, or electric commercial fleets.
- Test of service lifespan
- Test with high speed and torque
- Test for torque differential and speed differences
- Test of peak power
- Electrical to mechanical power efficiency test
- Torque interface to electric drive in the no-throttle test
- xCU interface to e-drive for the throttle test
- Test of the driving cycle
- Analysis of vibrations
- Thermal examinations:
-Cooling system stability test
-High-temperature operating endurance (Htoe)
-Powered thermal cycle endurance (Pájaro)
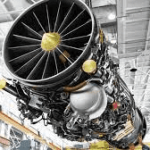
Solución de prueba aeroespacial
Proporcionamos los torquemeters, acoplamientos, volante, spindles & test rigs for both helicopter and aero engine component testing
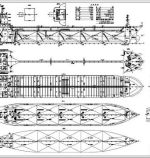
Solución de prueba marina
Proporcionamos una solución de prueba para motores marinos, sistemas de propulsión, motores eléctricos, conjuntos de generadores, cajas de cambios de transmisión, sistemas de energía auxiliar, sistemas de gases de escape, y repuestos para barcos
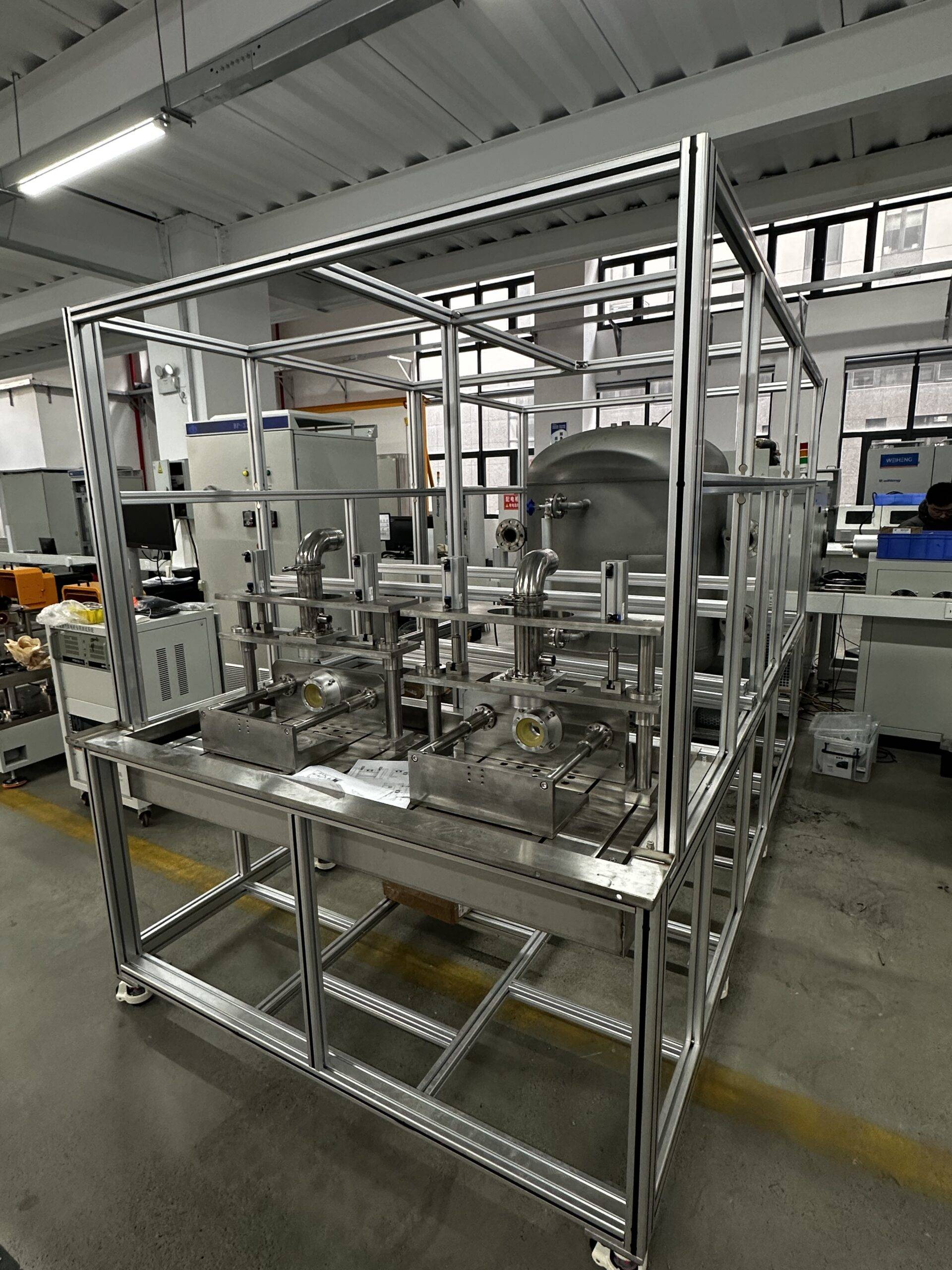
Banco de prueba de bomba de agua
El sistema de pruebas de bomba de agua es un equipo especializado utilizado para las pruebas de rendimiento de las bombas de agua, comúnmente utilizado para evaluar los parámetros clave como el flujo, cabeza, fuerza, y eficiencia.